500Kg/H - 600Kg/H Fish Feed Processing Machine
Main Machine: 1 screw, 2 sleeves, 3 molds (selected from 1.5-12mm), 1 electric heating plate, 1 set of blade holder, etc.
Pellet sizes: 1.5mm, 1.8mm, 2mm, 2.5mm, 3mm, 4mm, 5mm...... 12mm
Application: extruding fish/pet food pellets, suitable fish farms, pet food industries and feed manufacturing plant
Capacity: 500kg/h-600kg/h
Main Materials: most of machine is made of carbon steel, main part is made of stainless steel
Application
Extrusion processing is a processing technology that raw materials undergo high temperature, high pressure, and instantaneous curing. It integrates transportation, crushing, extrusion, mixing, shearing, high-temperature sterilization and molding. This raw material is incomparable with the general production technology, so fish feed puffing machine is more and more used in the production of high-end feed and food such as aquatic feed, pet feed and special breeding.
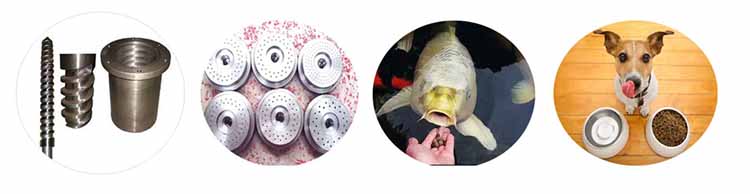
Features
Smooth and reliable and not easy to jam
Adopt inverter control to control the speed of the host
Under normal circumstances, when the machine is blocked, the inverter will start directly at a low speed.
Material in extruder barrel without disassembly
Neat, uniform and beautiful material
Can produce ultra-small diameter particles
Good uniformity
Has better self-cleaning effect
Many control parameters and easy to control
Forced slip away from the conveyed material
Applicable scope factory, can produce high oil and high moisture materials
Aquatic feed, pet feed and special animal feed
Weak shearing force
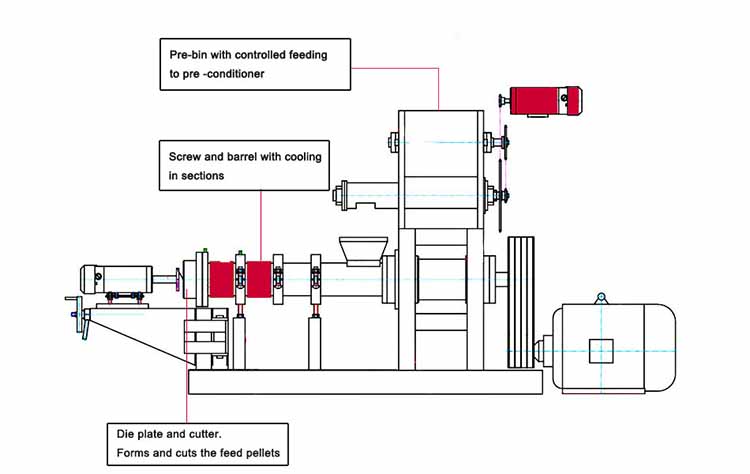
Feed pellets- Machine
1. With different parameters and feed formulation, fish farmers and feed plants can make floating, sinking and slow-sinking feed with high quality and nutrition so as to adapt for diverse ingestion requirements of various aquatic animals.
2. High temperature is to kill the germ
3. longer and easier storage period,
4. floating, sinking and slow sinking types, also can satisfy different demands of aquatic animals with various ingestion habits
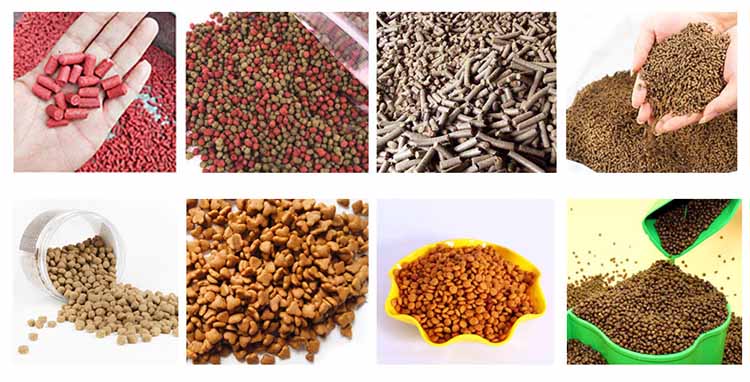
Parameters
Model | DGP120-B |
Main motor power | 55 KW |
Feeding power | 1.1 KW |
Cutting power | 1.5 KW |
Output | 500 - 600 KG / H |
Dimensions | 2400 * 1950 * 1600 mm |
Weight | 1700 KG |
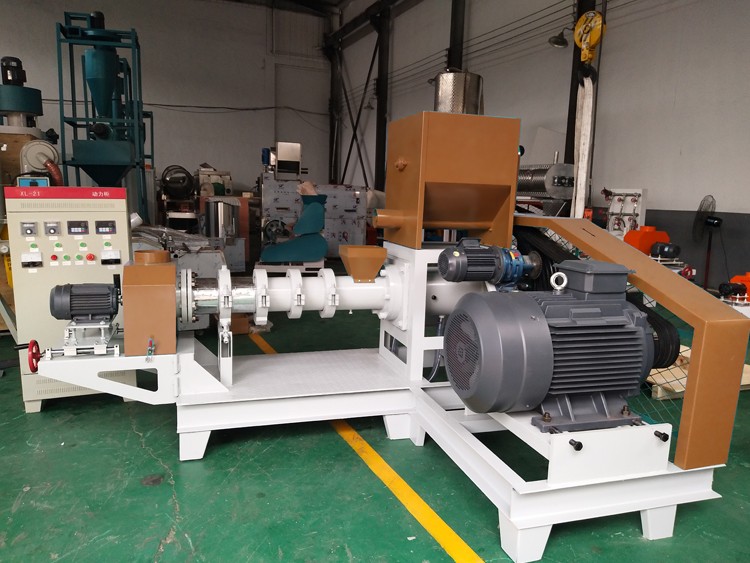
Working principle
In the conveying section, the material enters the barrel from the hopper, and with the rotation of the screw, it is transported forward along the direction of the screw groove, and is gradually compacted. After entering the compression and melting section, the pressure rises due to the changes in the spiral structure, and due to the heating of the barrel itself and the material between the two screws and the strong stirring, mixing and shearing of the screw and barrel, the temperature of the material rises High, start melting until all melt. As the space of the spiral groove is further reduced, the material is further heated and pressured to obtain cooking, so that the raw starch is fully gelatinized, and fat and protein are denatured. A series of complex biochemical reactions, such as tissue, are further homogenized to reach the uniform section. The material from the expansion cavity is evenly distributed to the template. At this time, the pressure is usually 3 ~ 6Mpa (depending on the expansion requirements), and the temperature can reach 150 ~ 200 掳 C. Because the high pressure in the closed sleeve exceeds the extrusion temperature Under the saturated vapor pressure, the moisture will not evaporate quickly. When the material is instantaneously squeezed out from the die hole of a certain shape, the pressure is released quickly, the free moisture evaporates rapidly, and the material expands accordingly. It is quickly cooled to about 80 掳 C, so it is cured and shaped, and maintains its expanded shape. 500Kg/H - 600Kg/H.
Reply comment